The global food supply chain is an intricate network, facing ever-increasing complexities and consumer demands for safer food. Traditional food safety management systems, while foundational, are being stretched to their limits. Enter Artificial Intelligence (AI), a transformative technology poised to revolutionize Hazard Analysis and Critical Control Points (HACCP) systems. By leveraging AI’s ability to analyze vast datasets, identify patterns, and predict outcomes, the food industry can achieve unprecedented levels of safety and efficiency. This article explores the burgeoning role of AI in HACCP, detailing its applications, benefits, and the future it promises for proactive food safety management.
AI-Powered HACCP: Ushering in a New Era of Food Safety and Risk Management
The integration of Artificial Intelligence into Hazard Analysis and Critical Control Points (HACCP) systems marks a significant leap forward in ensuring food safety. Traditional HACCP, a systematic preventive approach to food safety from biological, chemical, and physical hazards, relies heavily on human intervention and historical data. AI introduces dynamic, predictive, and data-driven capabilities that enhance every facet of the HACCP framework, leading to more robust risk management and a safer global food supply.
Understanding the Core: HACCP Principles and the AI Advantage
HACCP is built upon seven core principles designed to identify and control potential hazards at specific points in the food production process. AI can augment each of these principles:
- Principle 1: Conduct a Hazard Analysis.
- AI Application: AI algorithms, particularly machine learning (ML) and natural language processing (NLP), can rapidly analyze extensive databases of scientific literature, regulatory guidelines, historical recall data, and even social media trends to identify potential biological, chemical, and physical hazards far more comprehensively than manual methods. Predictive analytics can forecast emerging risks based on environmental factors, supplier history, and global food safety incidents.
- Principle 2: Determine the Critical Control Points (CCPs).
- AI Application: AI can analyze process flow diagrams and historical data to pinpoint the most effective CCPs. ML models can simulate different scenarios to identify points where control is absolutely essential to prevent, eliminate, or reduce a hazard to an acceptable level. This data-driven approach can optimize CCP selection, moving beyond reliance solely on expert opinion.
- Principle 3: Establish Critical Limits.
- AI Application: For each CCP, AI can help establish more precise and dynamic critical limits. By analyzing real-time sensor data (e.g., temperature, pH, time), AI can identify optimal boundaries that, if exceeded, indicate a deviation. This allows for tighter control and reduces the margin for error.
- Principle 4: Establish Monitoring Procedures.
- AI Application: AI-powered sensor networks and computer vision systems can automate and enhance CCP monitoring. For instance, cameras equipped with AI can continuously monitor hygiene practices, detect foreign objects, or verify labeling accuracy. Internet of Things (IoT) devices can stream real-time data from critical equipment (refrigerators, ovens) to AI platforms that flag any deviations instantaneously.
- Principle 5: Establish Corrective Actions.
- AI Application: When a deviation occurs, AI can recommend or even automate corrective actions. Based on the nature and severity of the deviation, AI systems can suggest specific steps to regain control of the process, minimize product loss, and ensure affected product is appropriately handled, drawing from a knowledge base of best practices and regulatory requirements.
- Principle 6: Establish Verification Procedures.
- AI Application: AI can streamline and improve the verification process. This includes analyzing monitoring records, calibration data, and corrective action reports to ensure the HACCP plan is working effectively. AI can identify anomalies or trends that might indicate a weakening in the system, prompting proactive review and adjustment. Predictive maintenance for monitoring equipment can also be scheduled by AI, ensuring their continued accuracy.
- Principle 7: Establish Record-Keeping and Documentation Procedures.
- AI Application: AI significantly enhances data management and documentation. Automated data logging from sensors and AI-driven analysis reduces manual data entry errors and creates a comprehensive, easily searchable digital audit trail. NLP can assist in standardizing and managing documentation, making compliance reporting more efficient. Blockchain technology, often coupled with AI, can provide immutable and transparent records throughout the supply chain.
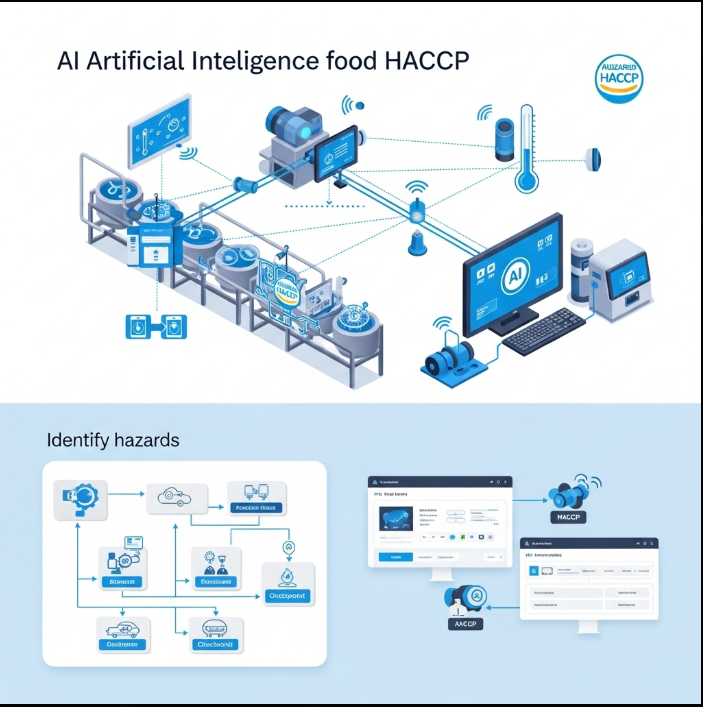
Tangible Benefits: How AI Elevates Food Safety and Risk Management in HACCP
The adoption of AI in HACCP offers a multitude of benefits for food businesses, regulators, and consumers:
- Enhanced Predictive Capabilities and Proactive Risk Management: AI’s ability to analyze vast datasets and identify subtle patterns allows for the prediction of potential hazards before they occur. This shifts HACCP from a reactive to a proactive risk management model, preventing food safety incidents rather than just responding to them. This includes predicting microbial growth, identifying potential allergen cross-contamination, or forecasting equipment failure that could impact a CCP.
- Improved Accuracy and Efficiency: Automated monitoring and data analysis through AI reduce human error and allow for continuous oversight of CCPs. This leads to more accurate data collection and faster identification of deviations, improving the overall efficiency of the HACCP system.
- Real-Time Monitoring and Rapid Response: AI-powered sensors and systems provide real-time insights into critical parameters. Alerts for deviations are instantaneous, enabling swift corrective actions that minimize the scope of potential food safety issues and reduce product waste.
- Optimized Resource Allocation: By identifying the highest risk areas and automating routine monitoring tasks, AI allows food safety professionals to focus their expertise on more complex challenges and strategic improvements.
- Enhanced Traceability and Transparency: AI, often in conjunction with technologies like blockchain, can create highly detailed and transparent records of the entire food production process. This improves traceability, which is crucial during food recalls or investigations into foodborne illness outbreaks.
- Reduction in Food Waste: By enabling more precise control over production processes and predicting potential spoilage, AI can help reduce food waste, a significant economic and environmental concern.
- Compliance and Regulatory Adherence: AI-driven record-keeping and reporting simplify compliance with stringent food safety regulations. The detailed audit trails generated by AI systems provide robust evidence of due diligence.
Specialized AI Technologies in Action within HACCP
Several specific AI technologies are making significant inroads into HACCP implementation:
- Machine Learning (ML): ML algorithms are used for predictive analytics, anomaly detection (e.g., unusual temperature fluctuations), image recognition (e.g., identifying contaminants or defects on a production line), and risk scoring.
- Computer Vision: AI-powered cameras can monitor employee hygiene, detect foreign objects, assess product quality (e.g., color, size, shape), and ensure correct labeling and packaging.
- Natural Language Processing (NLP): NLP can analyze unstructured data sources like supplier documentation, audit reports, and scientific papers to extract relevant information for hazard analysis and regulatory compliance. It can also power chatbots for instant access to HACCP procedures.
- Internet of Things (IoT) and AI: IoT sensors collect vast amounts of real-time data from various points in the food production environment (e.g., temperature, humidity, pH). AI algorithms then process this data to monitor CCPs, predict maintenance needs, and trigger alerts.
- Robotics and Automation: AI-controlled robots can perform repetitive tasks with high precision, such as cleaning and sanitation, sample collection, and even some aspects of food handling, reducing the risk of human contamination.
Navigating the Challenges: Considerations for AI Implementation in HACCP
Despite the compelling benefits, the integration of AI into HACCP systems is not without its challenges:
- Data Requirements and Quality: AI algorithms require large volumes of high-quality, relevant data to be trained effectively. Ensuring data integrity, accessibility, and standardization across the food supply chain can be a significant hurdle.
- Initial Investment Costs: Implementing AI solutions, including software, hardware (sensors, cameras), and the necessary infrastructure, can involve substantial upfront costs.
- Need for Specialized Expertise: Developing, implementing, and maintaining AI systems requires skilled data scientists, AI specialists, and food safety professionals trained in these new technologies.
- Integration with Existing Systems: Integrating new AI platforms with legacy IT systems within food processing facilities can be complex and time-consuming.
- Regulatory Acceptance and Standardization: While regulators are increasingly recognizing the potential of AI, clear guidelines and standards for validating AI-driven HACCP systems are still evolving.
- Ethical Considerations and Job Displacement: Concerns about data privacy and the potential for job displacement due to automation need to be addressed proactively.
The Future is Intelligent: AI as the Cornerstone of Next-Generation Food Safety
The trajectory of AI in HACCP is undeniably upward. Future developments are likely to include:
- More Sophisticated Predictive Models: AI will become even more adept at forecasting food safety risks with greater accuracy and longer lead times, incorporating a wider array of data sources, including genomic data for pathogen tracking and climate change impacts on agriculture.
- Hyper-Personalized Food Safety: AI could contribute to personalized risk assessments based on individual consumer vulnerabilities or preferences.
- Autonomous HACCP Systems: While human oversight will always be crucial, AI may automate more decision-making processes within the HACCP framework, particularly for routine operational controls.
- Enhanced Supply Chain Collaboration: AI-driven platforms will facilitate seamless data sharing and collaboration among all stakeholders in the food supply chain, leading to a more holistic and resilient food safety ecosystem.
- Democratization of AI Tools: As AI technology matures, more user-friendly and affordable AI solutions will become accessible to small and medium-sized enterprises (SMEs) in the food sector.
Conclusion:
Artificial Intelligence is not merely a futuristic concept in food safety; it is an increasingly vital tool for enhancing and evolving HACCP principles. By empowering food businesses with advanced analytical capabilities, real-time insights, and predictive power, AI strengthens risk management, improves efficiency, and ultimately contributes to a safer food supply for all. While challenges in implementation exist, the profound benefits of integrating AI into HACCP systems make it an indispensable component of future food safety strategies, paving the way for a more proactive, intelligent, and secure global food landscape.